Demand for pacchi batteria personalizzati has surged due to advancements in electric vehicles, renewable energy systems, and portable electronics. These solutions balance cost and performance to meet various industrial needs, from extending EV ranges to powering medical devices.
With the global custom battery pack market projected to grow at a 10.5% CAGR (reaching $22.43 billion by 2033), understanding their economic trade-offs is essential. This article explores how customization options, brand strategies, and material choices shape the cost-performance equation.
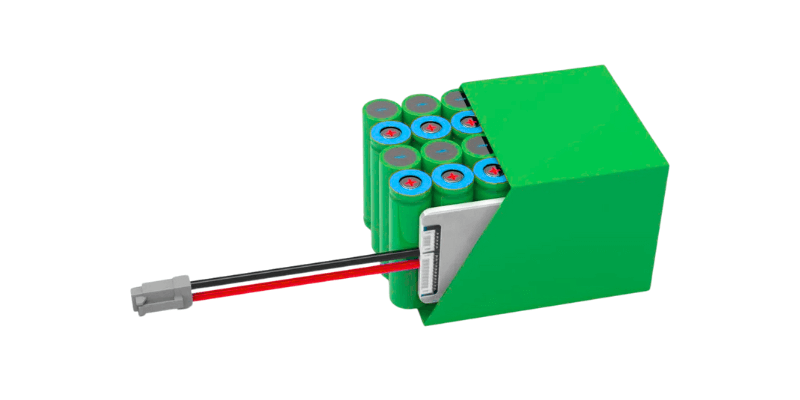
Battery Pack Customization Options
When customizing battery packs, preferences can vary. Some may choose a ready-made pack with a custom BMS, while others might prefer a custom battery cell with a standard BMS. It’s about finding what works best for each project.
Battery pack customization involves several factors, including:
Cell Chemistry Selection
The choice of battery chemistry determines key performance metrics like densità di energia, thermal stability, and lifecycle costs.
Lithium-ion batteries dominate due to their high energy density and cost-effectiveness. Solid-state batteries offer better safety but are expensive. Lead-acid and flow batteries serve niche applications requiring short-term, high-power output.
Connettori & wire assembly
High-current applications require precision-engineered interconnects:
- Terminal Types: Connectors like Anderson SB support 350A in EVs, while the MIL-DTL-38999 series offers EMI shielding for aerospace.
- Wire Harness Design: Automated crimping maintains contact resistance below 0.5 mΩ, with cross-sectional areas matched to current demands (e.g., 50 mm² for 200A).
- Material Science: Nickel-plated copper reduces oxidation, and silicone-insulated cables withstand temperatures from -40°C to 180°C.
Customization features modularity – Tesla’s structural battery packs use laser-welded busbars to reduce weight by 10% compared to bolted connections.
Holo Battery manufactures custom cables based on customer designs and specifications. We assist with cable and connector selection, layout, manufacturing techniques, and CAD. We also offer short-run manufacturing before mass production and handle all aspects, including soldering, termination, wrapping, and testing.
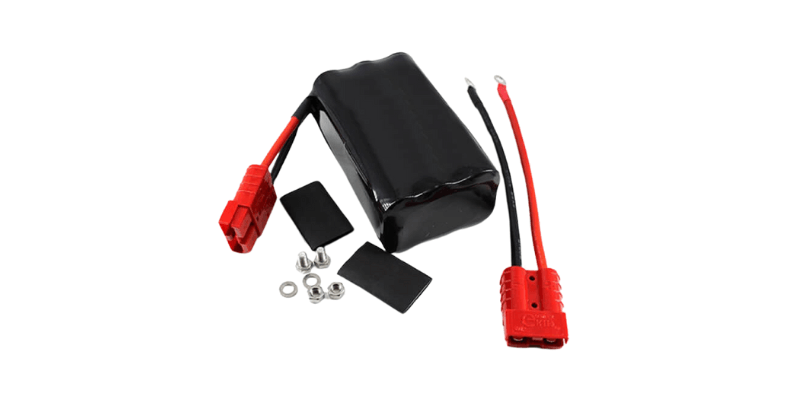
BMS components
At Holo Battery, we consider battery management systems (BMS) vital for monitoring key factors like voltaggio, current, temperature, and charge levels during operation. Our BMS stands out by integrating everything you need, including a precise battery gauge and safety features. We use a microcontroller to process data from our sensors and run specialized algorithms.
By collaborating with industry leaders, we create designs that are both safe and cost-effective.
Charging devices
Our all-in-one power management solution utilizes our expertise in custom battery chargers to keep your devices safe.
By refining the design of battery packs and chargers, manufacturers can increase charge rates, accurately determine when batteries are fully charged, and stop charging at the right time.
We have extensive experience with customized solutions using products from Texas Instruments, Microchip, Analog Devices, Seiko, and more to enhance charging speed and efficiency while extending battery lifespan.
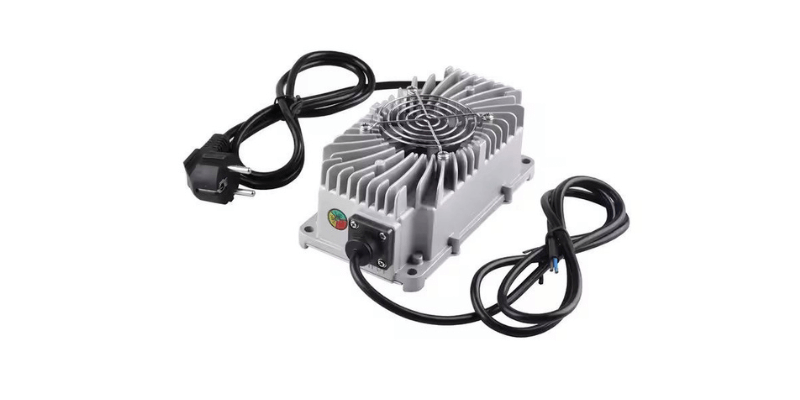
Power management integrated circuits (ICs)
Safety against overheating is important for lithium battery packs.
Primary safety circuits manage over-voltage, under-voltage, over-current, and temperature extremes. High-quality designs often include a secondary circuit for added protection if the primary fails.
Protection circuits in the Protection Circuit Module (PCM) should be tailored to specific applications; off-the-shelf PCMs are suitable only for lab prototypes. The PCM is part of the BMS, which monitors state, reports data, balances cells, protects the battery, and controls its environment.
Advanced applications use Integrated Circuits (ICs) with MOSFETs to switch lithium cells at upper current limits and may incorporate non-resettable protections in fail-safe environments.
Recinti & venting
Some battery packs are installed internally and require only a shrink-wrap enclosure, while others are externally mounted, potentially serving as a handle or base.
The enclosure must protect the cells and electronics from extreme temperatures, water, humidity, and vibration.
Here’s what you need to know about designing and managing custom battery pack enclosures.
Injection molded plastic enclosures are commonly used for battery packs, involving the molding of multiple plastic parts assembled with the pack and circuitry, sealed with glue, screws, or ultrasonic welding. Costs can be lowered by using insert moldings to integrate interconnection strips and terminali.
Shrink wrap or vacuum-formed plastic is a simple packaging solution for small batteries if enclosed by the final product.
Alternatively, external battery packs may serve functional roles like handles or bases. Our design experience enhances functionality while ensuring compliance with shock and environmental testing. Thermal effects must be considered; tolerances should allow for cell swelling up to 10%.
Enclosures may include vent holes to dissipate heat or exhaust gases. Intrinsically safe batteries prevent explosions in hazardous environments by using specific materials in their enclosures and potting material to fill air gaps.
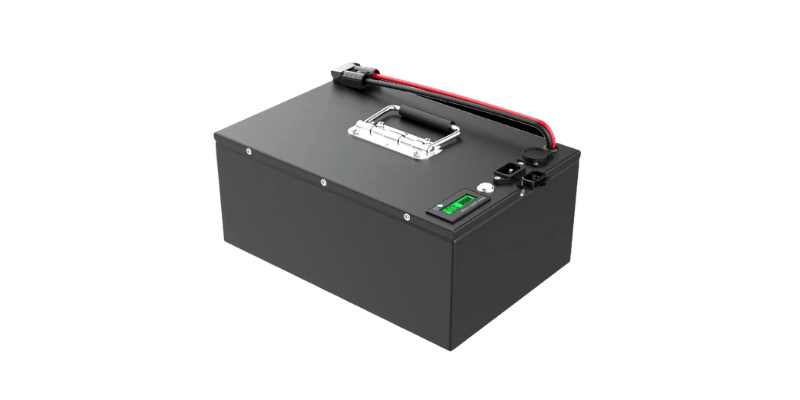
Battery Pack Brand Considerations
Brand is a crucial factor in the cost versus performance of custom battery packs. Battery brands range from low to high tier, with price differences based on cell type, chemistry, and electronics.
Basic packs offer standard electronics for charging and protection, while higher-end options include advanced features like fuel gauging, sleep mode, and state of health monitoring.
Application requirements significantly impact costs and performance; industries like medical, aerospace, and military often require specific safety features governed by standards or regulations.
Component and Material Factors
Customizations can involve ICs, connectors, enclosures, and other components, with material choices impacting costs. For instant, aluminum terminals are lightweight and cheaper but have lower strength and conductivity and are more prone to corrosion. In contrast, copper and gold-plated connectors offer better conductivity but are heavier and more expensive.
When selecting ICs, consider the charging profile and application requirements; types of charge (trickle, constant current/voltage, fast charging) affect safety features and configurations.
Charger topology depends on battery pack series, cell count, power management path, input voltage range, and safety features.
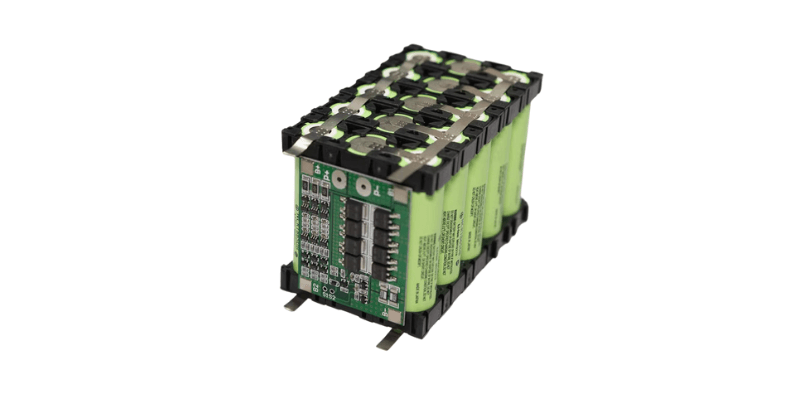
Conclusione
Extensive research is necessary to obtain a custom battery pack due to varying application requirements and battery brand costs. Understand the industry, component trends, material markets, and manufacturer capabilities to identify available customizations. Then, contact a manufacturer like Holo Battery to learn about new technologies and materials that can enhance design while remaining budget-friendly.