重要なポイント:
- リチウム電池のコストは、セル構成、電池管理システム、カスタムパック設計、テスト/認証などの要因によって影響されます。
- これらの要素を理解することは、費用を効果的に管理し、バッテリーのパフォーマンスを最適化するために重要です。
個人や法人が購入する場合 バッテリーパック, 経費は重要な焦点です。
2023 年の電気自動車バッテリー パックの平均コストは、 128ドル/kWh。これは、2008 年当時の価格 (1,355 ドル/kWh) よりも大幅に低いです。ただし、リチウム電池は電池化学コストの中で一貫して高額であることは注目に値します。
リチウム電池の価格はさまざまな要素によって影響されます。これらには、細胞自体、 バッテリー管理システム (BMS)、バッテリーパックシステム全体、テストおよび配送のコスト。
バッテリーセル
個々のバッテリーセルは総生産費の約 80% を占めます。バッテリーセルは、カソード、アノード、電解質、セパレーター、外装ケースなどのいくつかの部分で構成されています。
カソード材料とその製造プロセスは最も高価な要素となる傾向があり、アノードとセパレータのコストがそれに続きます。
カソードは主にリチウムとコバルト、ニッケル、またはマンガンのいずれかで構成されており、アノードには通常グラファイトが使用されます。これらの材料の市場価格は需要と供給に応じて変動する可能性があり、高性能エレクトロニクスや電気自動車に対する需要の増加により、これらの金属が不足しています。
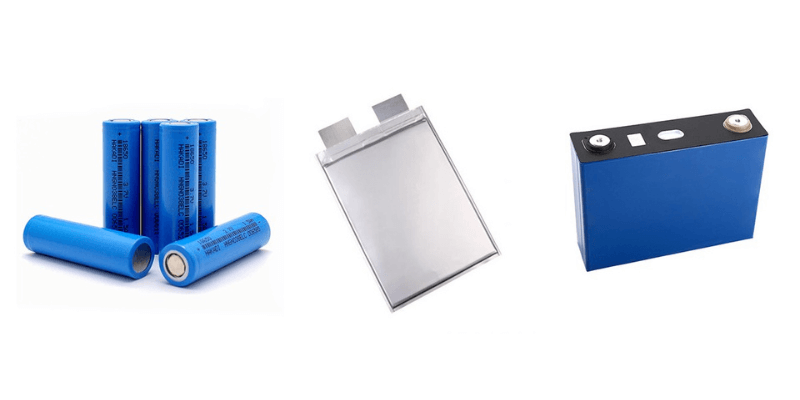
世界の資源の利用可能量は 2050 年までに減少すると予想されています。中国のリチウム供給に影響を与える熱波や、コンゴ民主共和国のコバルト採掘に関連する懸念などの問題により、環境問題と人権問題の両方が引き起こされています。
特定の地域での政情不安により、これらの材料を大量に確実に入手できる製造業者は限られており、サプライチェーンの混乱につながる可能性があります。
これらの要因がコストを押し上げている結果、メーカーはそれに応じてセルの価格を引き上げる可能性があります。
BMS
リチウム電池の保護および充電メカニズムは、電池パックの製造コストに大きな影響を与えます。
国際規制に従って、すべてのリチウムベースのバッテリーには BMS が装備されている必要があります。このシステムは、バッテリーの充電状態 (SoC) とその健康状態 (SoH) を監視し、過充電や過剰放電を防止してバッテリーを損傷から保護し、寿命を延ばす役割を担っています。
BMS のコストは、顧客がデバイスに必要とする機能によって異なります。基本的な BMS ユニットは、SoC、SoH、および温度を監視します。高度なユニットには、バッテリー バランシング、リアルタイム クロック、データ ロガーなどが含まれる場合があります。機能が増えると BMS コストが増加します。お客様が BMS に含める機能の適切なレベルを決定するには、電力要件を明確に理解することが不可欠です。

充電プロセス中に、バッテリー充電器内の集積回路 (IC) が利用されます。リニア充電器やスイッチモード充電器など、さまざまなタイプの IC が利用可能です。これらの IC はバッテリーを充電するだけでなく、過電圧や過電流に対する保護も提供します。
バッテリ充電器に関連する費用は、顧客がすぐに使用できるようにバッテリ パックに充電器を同梱することを好むか、エンドユーザーが独自の充電器を選択できるようにするかによって異なります。カスタム充電器と標準充電器の選択もコストに影響し、通常、カスタム充電器の方が高価です。
カスタムバッテリーパックシステム
バッテリー パック システムは、バッテリー エンクロージャと、ワイヤリング ハーネス、リレー、コネクタ、BMS ソフトウェア、加熱および冷却用の熱管理システムなどのさまざまなコンポーネントで構成されます。これらのコンポーネントにより、リチウム電池の電力をさまざまな機器に安定的に供給できます。
ワイヤリング ハーネス、コネクタ、BMS は標準コンポーネントですが、他の要素はさまざまなアプリケーションの特定のニーズを満たすように調整されています。
カスタム バッテリー パック システムを設計する過程で、追加のコンポーネントを追加すると、それに比例して製造コストも増加します。
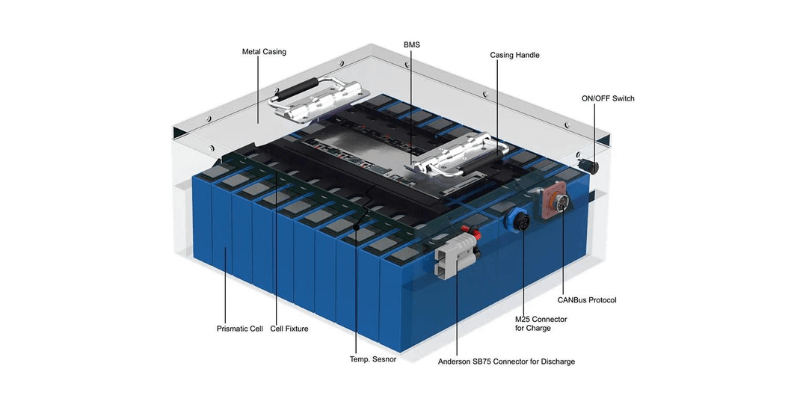
特定のコンポーネントを低コストの材料 (リレーなど) で置き換えると、全体的なパフォーマンスとバッテリー寿命に影響を与える可能性があることに注意することも重要です。お客様は、バッテリーパックシステムの設計および製造コストと、その性能および品質とのバランスを考慮する必要があります。
場合によっては、初期費用が高くても高品質のバッテリー パック システムを選択すると、バッテリーの耐久性が向上するため、長期的な節約につながる可能性があります。
テストと出荷
リチウム電池パックのメーカー 輸送前にリチウム電池パックの安全性を認証する必要があります。
CE などの一部の認定は社内で行われます。外部のラボが必要な場合もあります。費用は、認定の種類に応じて、500 ドルから 30,000 ドルの範囲です。サンプル パックは、破壊テストと非破壊テストの両方に必要です。
テストが失敗した場合は再設計が必要になる可能性があり、新しい設計も認定される必要があるためコストが増加します。メーカーを変更すると、たとえ同じ設計であっても、再テストと再認定が必要になる場合があります。お客様は、リチウム電池のテスト、認証、および輸送要件について常に予算を立てる必要があります。
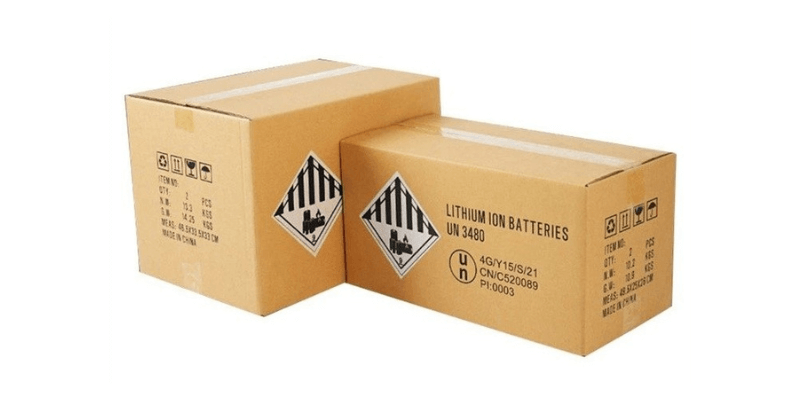
結論
現在、リチウム電池の設計および製造コストは、他の種類の化学電池よりも高くなります。
しかし、技術の進歩が続く中、メーカーは、さまざまなデバイスに提供する電力を犠牲にすることなく、これらの化学組成をよりコスト効率の高いものにするために積極的に取り組んでいます。
バッテリーパックと充電器のカスタマイズを検討している人にとって、アプリケーションの正確な電力需要を理解することは非常に重要です。設計段階でメーカーに包括的なドキュメントを提供すると、よりコスト効率の高いソリューションが得られます。設計プロセスの最初からメーカーと協力することも、製造上の課題を軽減し、無駄を削減するのに役立ち、最終的にはよりコスト効率の高い結果につながります。