Viktige takeaways:
- Kostnaden for litiumbatterier påvirkes av faktorer inkludert cellesammensetning, batteriledelsessystemer, tilpasset pakkedesign og testing/sertifisering.
- Å forstå disse elementene er avgjørende for å effektivt administrere utgifter og optimalisere batteriets ytelse.
Når enkeltpersoner eller bedrifter kjøper batteripakker, utgiftene er et sentralt fokuspunkt.
I 2023 er den gjennomsnittlige kostnaden for en batteripakke for elektrisk kjøretøy i 2023 $ 128/kWh. Dette er betydelig lavere enn prisen tilbake i 2008, som var $ 1.355/kWh. Imidlertid er det verdt å merke seg at litiumbatterier konsekvent har vært i den høyere enden av batteriets kjemikostnader.
Prisen på litiumbatterier påvirkes av en rekke elementer. Disse inkluderer selve cellen, batteristyringssystem (BMS), det samlede batteripakke -systemet, testing og fraktkostnader.
Batterisceller
De individuelle batteriscellene representerer omtrent 80% av de totale produksjonsutgiftene. En batteriscelle er sammensatt av flere deler: katoden, anoden, elektrolytten, separatoren og det ytre foringsrøret.
Katodematerialer og deres produksjonsprosesser har en tendens til å være de dyreste elementene, med kostnadene for anoder og separatorer som følger tett bak.
Katoden består hovedsakelig av litium kombinert med enten kobolt, nikkel eller mangan, mens grafitt vanligvis brukes til anoden. Markedsprisene for disse materialene kan variere basert på tilbud og etterspørsel, og den økende etterspørselen etter elektronikk med høy ytelse og elektriske kjøretøyer har resultert i en mangel på disse metallene.
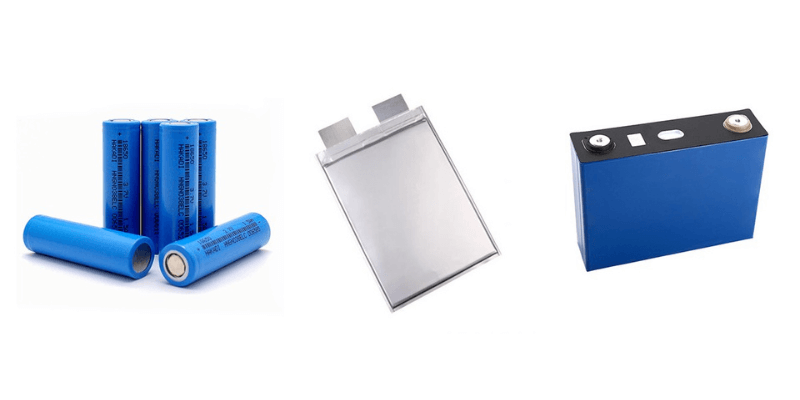
Det er forventet at tilgjengeligheten av globale ressurser vil avta innen år 2050. Problemer som hetebølger som påvirker litiumforsyninger i Kina og bekymringer relatert til koboltgruvepraksis i Den demokratiske republikken Kongo har reist både miljø- og menneskerettighetsspørsmål.
På grunn av politisk uro i visse regioner har produsenter i bare noen få land pålitelig tilgang til store mengder av disse materialene, noe som fører til potensielle forstyrrelser i forsyningskjeden.
Som et resultat av disse faktorene som øker kostnadene, vil produsentene sannsynligvis øke celleprisene som svar.
BMS
Beskyttelses- og lademekanismene for litiumbatterier påvirker produksjonskostnadene for batteripakker betydelig.
I tråd med internasjonale forskrifter, må alle litiumbaserte batterier være utstyrt med en BMS. Dette systemet har til oppgave å overvåke batteriets ladetilstand (SOC) og dets helsestatus (SOH), ivareta batteriet mot skade og forlenge levetiden ved å forhindre overlading eller overdreven utslipp.
Kostnaden for BMS avhenger av funksjonene kundene krever på enhetene sine. Grunnleggende BMS -enheter overvåker SOC, SOH og temperatur. Avanserte enheter kan omfatte batteribalansering, sanntidsklokker, dataloggere og mer. Flere funksjoner øker BMS -kostnadene. En klar forståelse av strømkravene er avgjørende for at kundene skal bestemme det aktuelle nivået av funksjoner som skal inkluderes i BMS.

Under ladeprosessen brukes integrerte kretser (ICS) i batteriladeren. Det er forskjellige typer IC-typer, for eksempel lineære ladere og switch-modusladere. Disse IC -ene lader ikke bare batteriet, men gir også beskyttelse mot overspenning og overstrøm.
Utgiftene forbundet med batteriladere er avhengig av om kundene foretrekker å ha ladere med batteripakken for øyeblikkelig bruk eller la sluttbrukere velge sine egne ladere. Valget mellom tilpassede og standardladere påvirker også kostnadene, med tilpassede ladere som vanligvis er dyrere.
Tilpasset batteripakkesystem
Batteripakke -systemet er sammensatt av et batterikabinett og en rekke komponenter, inkludert ledningsnett, reléer, kontakter, BMS -programvare og termiske styringssystemer for oppvarming og kjøling. Disse komponentene sikrer stabil strømforsyning av litiumbatterier til forskjellige enheter.
Mens ledningsnett, kontakter og BMS er standardkomponenter, er andre elementer skreddersydd for å imøtekomme de spesifikke behovene til forskjellige applikasjoner.
I prosessen med å designe et tilpasset batteripakkesystem, vil det å legge til ekstra komponenter proporsjonalt øke produksjonskostnadene.
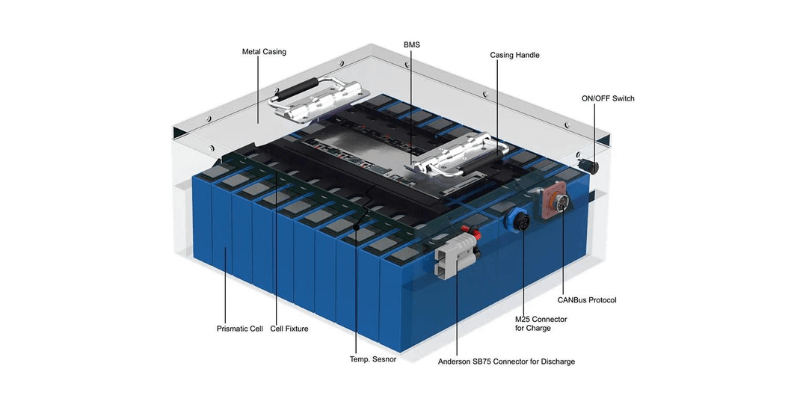
Det er også viktig å merke seg at å erstatte visse komponenter med lavere kostnadsmaterialer (for eksempel reléer) kan påvirke den generelle ytelsen og batterilevetiden. Kunder bør vurdere balansen mellom design- og produksjonskostnadene for batteripakningssystemet og dets ytelse og kvalitet.
I noen tilfeller kan det å velge et batteripakkesystem av høyere kvalitet, til tross for de høyere forhåndskostnadene, føre til langsiktig besparelse på grunn av den forbedrede holdbarheten til batteriet.
Testing og frakt
Litiumbatteripakkeprodusenter Må sertifisere litiumbatteripakker for sikkerhet før transport.
Noen sertifiseringer, som CE, gjøres internt; Andre krever eksterne laboratorier. Kostnadene varierer fra $ 500 til $ 30 000, avhengig av sertifiseringstypen. Eksempelpakker er nødvendig for både destruktive og ikke-destruktive tester.
Det kan være nødvendig med redesign hvis tester mislykkes, og øker kostnadene ettersom nye design også må sertifiseres. Bytteprodusenter, selv med samme design, kan kreve retesting og resertifisering på nytt. Kunder bør alltid budsjettere for litiumbatteritesting, sertifisering og transportkrav.
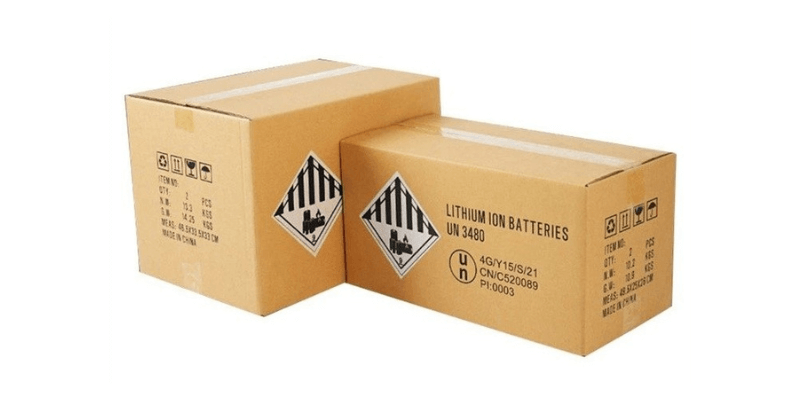
Konklusjon
Foreløpig er design- og produksjonskostnadene for litiumbatterier høyere enn for andre typer kjemiske batterier.
Imidlertid, med pågående teknologiske fremskritt, jobber produsentene aktivt for å gjøre disse kjemiske sammensetningene mer kostnadseffektive uten at det går ut over kraften de gir til forskjellige enheter.
For de som ønsker å tilpasse batteripakker og ladere, er det avgjørende å forstå de nøyaktige strømkravene til applikasjonene. Å gi produsenter omfattende dokumentasjon i designfasen kan føre til mer kostnadseffektive løsninger. Å engasjere produsenter fra begynnelsen av designprosessen kan også bidra til å dempe produksjonsutfordringer og redusere avfall, og til slutt føre til mer kostnadseffektive utfall.