O design e a produção de bateria personalizada Os gabinetes plásticos requerem atenção cuidadosa aos detalhes para garantir a funcionalidade, a segurança e a conformidade com os padrões do setor. Você precisa considerar tudo – Da conformidade e seleção de materiais à marca eficaz. Aqui estão alguns pontos -chave a serem lembrados ao desenvolver um gabinete de bateria personalizado.
Navegando requisitos regulatórios e de design
Muitos clientes não estão familiarizados com os regulamentos de segurança da bateria, o que pode levar a atrasos ou redesenhos. Um fabricante deve primeiro esclarecer o escopo do projeto – Se envolve a propriedade completa ou parcial do design.
A colaboração completa permite o gerenciamento de arquivos CAD, prototipagem, teste e planejamento de produção, reduzindo revisões caras. Os custos e os cronogramas de ferramentas devem se alinhar com a escala do projeto, enfatizando a necessidade de precisão na fase inicial do projeto.
Certificações de segurança de transporte, como E 38,3 Para baterias de lítio, são essenciais. Os gabinetes devem suportar testes de queda, Extremos de temperaturae simulações de vibração para atender a esses padrões.
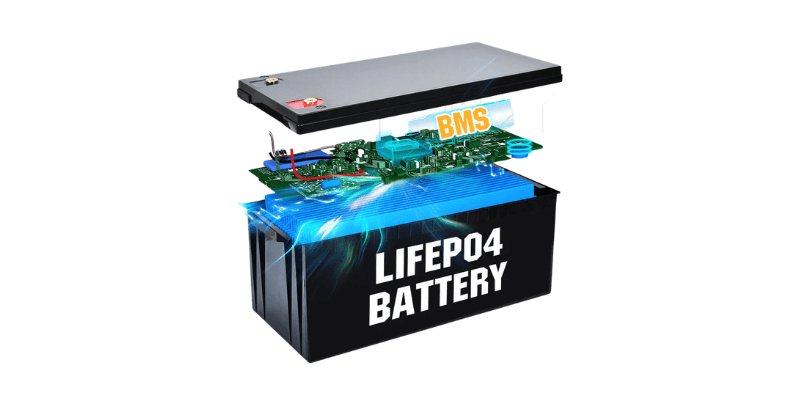
Seleção de materiais e fatores ambientais
A escolha do grau plástico depende do ambiente do aplicativo.
Por exemplo, o plástico ABS é econômico, mas quebradiço em resfriado extremo, enquanto as misturas de policarbonato (PC) ou híbridas oferecem maior durabilidade para condições adversas.
Fatores ambientais, como umidade, exposição a UV e estresse mecânico, devem orientar a seleção de material, juntamente com testes de queda e requisitos de certificação para refinar as decisões.
Branding e personalização estética
A marca transforma uma parte básica em algo comercializável.
As opções incluem adicionar rótulos ou usar impressão digital para logotipos e avisos. A gravura a laser é ideal para um acabamento permanente e durável.
A estética personalizada garante que o gabinete alinhe com a identidade da marca do cliente, mantendo a integridade estrutural.

Métodos de vedação e montagem
Selando o gabinete é importante para proteger internos componentes. Alguns métodos populares para conseguir isso incluem:
- Soldagem ultrassônica: esta técnica rápida usa vibrações de alta frequência para derreter e unir o plástico sem cola.
- Fixadores mecânicos: parafusos ou parafusos permitem fácil acesso para reparos, mas podem representar um risco se a violação for uma preocupação.
- Adesivos: ideal para pequenos lotes, mas menos robustos para aplicações de alto estresse.
Proteger componentes internos
Para abordar as preocupações sobre a mudança de componentes internos, existem opções para proteger peças no local. As soluções incluem:
- Preenchimento de espuma ou silicone RTV para absorver choques.
- Projetos com nervuras ou combinações de cola para travar as peças no lugar.
Depois que os detalhes do produto são claros, o design do gabinete interno pode começar.
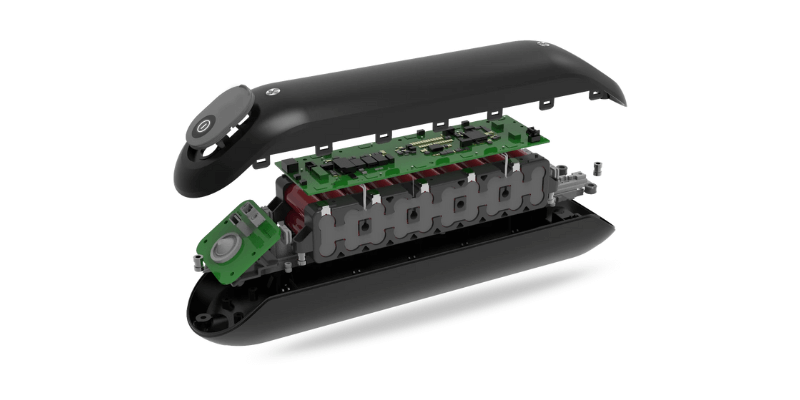
Circuitos de segurança para baterias de lítio
As baterias de íon de lítio requerem uma segurança integrada PCB (Placa de circuito impresso) ou BMS (Sistema de Gerenciamento da Bateria) para evitar riscos, como sobrecarga, curto -circuitos e desequilíbrio celular.
Uma PCB de segurança ou BMS monitora a tensão, a corrente e a temperatura, garantindo que todas as células operem dentro de limites de segurança e permaneçam equilibrados. O não cumprimento desses requisitos pode resultar em falhas de certificação e aumentar o risco de incidentes de segurança.
Atualizando os designs existentes
A modernização das baterias desatualizadas normalmente envolve a mudança para químicas de lítio ou novos formatos de células, como cilíndricos para prismáticos.
Os gabinetes existentes de engenharia reversa podem reduzir custos, mas um novo design pode ser necessário para restrições de espaço ou desempenho aprimorado.

Conclusão
O projeto de gabinete de bateria personalizado de sucesso depende da colaboração entre o cliente e fabricante. Engajamento precoce, comunicação clara das necessidades ambientais e adesão aos padrões de segurança otimizam o processo. A compreensão desses elementos ajuda os clientes a tomar decisões informadas que otimizam o desempenho, o custo e a conformidade regulatória.