ประเด็นสำคัญ:
- การเลือกผู้ผลิตแบตเตอรี่ลิเธียมแบตเตอรี่ต้องมีการประเมินความสามารถอย่างพิถีพิถันคุณภาพการปฏิบัติตามข้อกำหนดความมั่นคงทางการเงินและการกำหนดราคา จัดลำดับความสำคัญประสิทธิภาพปัจจัยด้านสิ่งแวดล้อมการรับรองและวิสัยทัศน์ที่ใช้ร่วมกันสำหรับการเป็นหุ้นส่วนที่แข็งแกร่ง
ตามความต้องการ แบตเตอรี่ลิเธียมไอออน เติบโตแบบทวีคูณเลือกที่ผ่านการรับรองอย่างถูกต้อง ผู้ผลิตชุดแบตเตอรี่ลิเธียม เป็นสิ่งสำคัญสำหรับ บริษัท ที่ต้องการรวมเทคโนโลยีหลักนี้เข้าด้วยกัน
ในคู่มือที่ครอบคลุมนี้เราจะสำรวจปัจจัยสำคัญที่ควรพิจารณาเมื่อเลือกซัพพลายเออร์แบตเตอรี่ลิเธียมไอออน
การกำหนดข้อกำหนดการจัดหา
ขั้นตอนแรกคือการทำความเข้าใจอย่างชัดเจนเกี่ยวกับข้อกำหนดของแบตเตอรี่ลิเธียมไอออนโดยเฉพาะของคุณ:
- ปัจจัยด้านประสิทธิภาพ - ความสามารถที่ต้องการ แรงดันไฟฟ้า, อัตรา C, วัฏจักรชีวิต, การสูญเสียตนเองที่ยอมรับได้
- ปัจจัยทางกายภาพ - ฟอร์มแฟคเตอร์ที่ต้องการขนาดข้อ จำกัด น้ำหนัก
- ปัจจัยด้านสิ่งแวดล้อม - ช่วงอุณหภูมิ, การสั่นสะเทือน, ความต้องการความต้านทานต่อการกระแทก
- คุณภาพและความน่าเชื่อถือ - ความคาดหวังที่สอดคล้องกันอัตราข้อบกพร่องข้อกำหนดความล้มเหลวของภาคสนาม
- ความต้องการการรับรอง - ความปลอดภัย, กฎระเบียบ, มาตรฐานการปฏิบัติตามกฎระเบียบเช่น UL 1642 หรือ และ 38.3
- ปริมาณการสั่งซื้อ - ความต้องการมาตราส่วนการผลิตและความยืดหยุ่น
- เป้าหมายต้นทุน - ข้อกำหนดด้านราคาและความเต็มใจที่จะจ่ายเบี้ยประกันเพื่อคุณภาพ
- เวลา - กรอบเวลาการพัฒนาและอัตราการผลิตทางลาด
การจัดลำดับความสำคัญของพารามิเตอร์ที่สำคัญที่สุดของคุณจะมุ่งเน้นการค้นหาของคุณเฉพาะผู้ผลิตที่สามารถส่งมอบผลิตภัณฑ์ที่ตอบสนองความต้องการของคุณได้
การประเมินความสามารถในการผลิต
ตรวจสอบความสามารถในการผลิตแบตเตอรี่ลิเธียมแบตเตอรี่ที่มีศักยภาพอย่างระมัดระวัง:
- กำลังการผลิต - พวกเขาสามารถสร้างปริมาณที่เพียงพอเพื่อตอบสนองความต้องการในปัจจุบันและที่คาดการณ์ไว้หรือไม่? ผลลัพธ์สูงสุดของพวกเขาคืออะไร?
- รูปแบบเซลล์ - พวกเขาเสนอรูปแบบทรงกระบอก, กระเป๋า, ปริซึมหรือรูปแบบที่กำหนดเองหรือไม่?
- Chemistries - พวกเขาสามารถจัดหาลิเธียมโคบอลต์ออกไซด์ (LCO) ที่คุณต้องการ (LCO), ลิเธียมแมงกานีสออกไซด์ (LMO), ลิเธียมเหล็กฟอสเฟต (LFP), ลิเธียมนิกเกิลแมงกานีสโคบอลต์ออกไซด์ (NMC), ลิเธียมนิกเกิลอลูมิเนียมออกไซด์ (NCA)
- กระบวนการคุณภาพ - มาตรฐานการควบคุมคุณภาพและขั้นตอนใดที่ดำเนินการในระหว่างการผลิต
- ร&D ความสามารถ - พวกเขามี R ที่แข็งแกร่งหรือไม่&ทีมพัฒนาเทคโนโลยีเซลล์รุ่นต่อไปหรือไม่? พวกเขาสามารถปรับแต่งเซลล์ตามความต้องการของคุณได้หรือไม่?
- ในบ้านเทียบกับภายนอก-เปอร์เซ็นต์ของการผลิตที่จัดการภายในเทียบกับภายนอก?
- การรับรอง - สิ่งอำนวยความสะดวกและผลิตภัณฑ์ของพวกเขาได้รับการรับรองตามมาตรฐานที่จำเป็นเช่น ISO 9001, IATF 16949, UL 1642 หรือไม่?
- ระบบอัตโนมัติ - การใช้งานอัตโนมัติในระดับใด ระบบอัตโนมัติที่สูงขึ้นช่วยเพิ่มความสอดคล้อง
- สถานที่ผลิต - โรงงานผลิตของพวกเขาอยู่ที่ไหน? ความใกล้ชิดสามารถช่วยโลจิสติกส์ห่วงโซ่อุปทาน
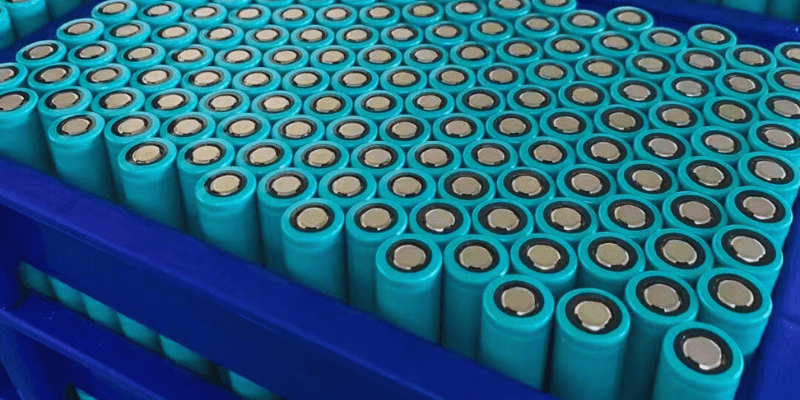
การเลือกผู้ผลิตแสดงให้เห็นถึงความสามารถอย่างชัดเจนในการตอบสนองข้อมูลจำเพาะของคุณจะช่วยลดความล่าช้าและปัญหาที่อาจเกิดขึ้น
ประเมินประสบการณ์อุตสาหกรรมของพวกเขา
ประสบการณ์ที่เกี่ยวข้องโดยตรงของซัพพลายเออร์คือการคาดการณ์ประสิทธิภาพที่คาดหวัง:
- ปีในธุรกิจ-พวกเขาผลิตแบตเตอรี่ลิเธียมไอออนมานานแค่ไหน? ประวัติศาสตร์ที่ยาวนานขึ้นสะท้อนถึงความมั่นคงและความรู้
- พอร์ตโฟลิโอลูกค้า-พวกเขาจัดหาแบตเตอรี่ลิเธียมไอออนหรือเซลล์ให้กับ OEM ที่สำคัญและมีชื่อเสียงหรือไม่? ลูกค้าระดับ 1 ขนาดใหญ่ระบุความไว้วางใจในซัพพลายเออร์
- อัตราความล้มเหลวของภาคสนาม - อัตราข้อบกพร่องพื้นหลังหรือการเรียกร้องการรับประกันของพวกเขาคืออะไร? ต่ำกว่าดีกว่า
- ทีมผู้บริหาร-ผู้จัดการอาวุโสมีพื้นฐานที่แข็งแกร่งในการพัฒนาและผลิตเซลล์ลิเธียมไอออนหรือไม่? ความเชี่ยวชาญอย่างลึกซึ้งช่วยปรับปรุงผลลัพธ์
- พนักงาน-พนักงานมีประสบการณ์การทำงานโดยเฉพาะกับสายแบตเตอรี่ลิเธียมไอออนหรือไม่? ทักษะพิเศษเป็นที่ต้องการ
- การทดสอบวัฏจักรชีวิต - พวกเขาสามารถตรวจสอบวัฏจักรชีวิตอย่างละเอียดเพื่อมาตรฐานมาตรฐานสำหรับแอปพลิเคชันของคุณได้หรือไม่?
- การทดสอบความปลอดภัย - พวกเขาทำการทดสอบอย่างเข้มงวดเพื่อรับรองความปลอดภัยและความน่าเชื่อถือหรือไม่?
ความเชี่ยวชาญของเรื่องที่มากขึ้นทำให้ผู้ผลิตมีความเป็นไปได้มากขึ้นจะเป็นไปตามความคาดหวัง
ประเมินการตอบสนองและการสนับสนุน
ความสามารถของผู้ผลิตในการให้การสนับสนุนที่ตอบสนองในระหว่างการพัฒนาและการผลิตมีความสำคัญ:
- ความคล่องตัวต้นแบบ - พวกเขาสามารถให้ต้นแบบหรือตัวอย่างได้เร็วแค่ไหน?
- การปรับแต่ง-พวกเขาสามารถปรับแต่งแบตเตอรี่ลิเธียมไอออนเพื่อตอบสนองประสิทธิภาพที่แน่นอนของคุณฟอร์มแฟคเตอร์หรือความต้องการการเชื่อมต่อหรือไม่?
- เปลี่ยนที่พัก - พวกเขาสามารถปรับเปลี่ยนผลิตภัณฑ์ได้อย่างไร?
- การสนับสนุนการพัฒนา - พวกเขาจะให้การสนับสนุนด้านวิศวกรรมโดยตรงในระหว่างการพัฒนาผลิตภัณฑ์ของคุณหรือไม่?
- บริการหลังการขาย-พวกเขามีเจ้าหน้าที่ด้านเทคนิคสำหรับการแก้ไขปัญหาและการแก้ไขปัญหาหลังการซื้อหรือไม่?
- กระบวนการคุณภาพ - พวกเขาสามารถแบ่งปันการลดข้อบกพร่องโดยละเอียดและกระบวนการดำเนินการแก้ไขได้หรือไม่?
- เอกสาร - พวกเขาจะจัดเตรียมแผ่นข้อมูลเซลล์/แพ็คที่ครอบคลุมรุ่นโมเดลรายงานการรับรองหรือไม่?
- ความมั่นคงทางธุรกิจ-พวกเขาแสดงความมั่นคงทางการเงินในระยะยาวหรือไม่?
การเลือกผู้ผลิตแบตเตอรี่ลิเธียมสามารถร่วมมือกับทีมของคุณได้อย่างคล่องแคล่วช่วยให้การพัฒนาอย่างราบรื่นและบรรเทาการหยุดชะงักของโปรแกรม
กระบวนการตรวจสอบบัญชีและสิ่งอำนวยความสะดวก
การตรวจสอบสิ่งอำนวยความสะดวกกระบวนการและการจัดการของผู้ผลิตอย่างจริงจังให้ความมั่นใจในคุณภาพการผลิต:
- ทัวร์สถานที่ - เยี่ยมชมโรงงานเป็นการส่วนตัวเพื่อตรวจสอบโครงสร้างพื้นฐานความสะอาดและเวิร์กโฟลว์
- ร&D และการทดสอบ - ทบทวนการออกแบบเซลล์การขี่จักรยานกระบวนการรับรองความปลอดภัย
- การตรวจสอบที่เข้ามา - ตรวจสอบการตรวจสอบวัตถุดิบและขั้นตอนการยอมรับ
- การผลิตเซลล์ - สังเกตการเคลือบอิเล็กโทรด, ม้วน, ซ้อน, ขั้นตอนการเชื่อมแท็บ
- การปรับสภาพของเซลล์ - ประเมินค่าเริ่มต้น/การปลดปล่อยเริ่มต้นอายุและกระบวนการให้คะแนน
- การควบคุมคุณภาพ - ตรวจสอบการควบคุมกระบวนการตรวจสอบข้อบกพร่องและการดำเนินการแก้ไข
- การตรวจสอบขาออก - ยืนยันขั้นตอนการทดสอบแพ็คและเซลล์เสร็จแล้ว
- ระบบ ERP - ตรวจสอบความสามารถในการจัดตารางการผลิตและการตรวจสอบย้อนกลับ
- ความสามารถของพนักงาน - การฝึกอบรมมาตรวัดความถนัดทางเทคนิคและประสบการณ์ของพนักงานชั้น
- มาตรฐานความปลอดภัย - ตรวจสอบให้แน่ใจว่ามีโปรโตคอลความปลอดภัยในการผลิตแบตเตอรี่
การเยี่ยมชมซัพพลายเออร์ให้การประเมินที่ดีที่สุดเกี่ยวกับความมั่นคงและความเป็นมืออาชีพ การตรวจสอบสร้างความโปร่งใสและความไว้วางใจ
การตรวจสอบการปฏิบัติตามและการรับรอง
ยืนยันการรับรองแบตเตอรี่ลิเธียมที่สำคัญทั้งหมดได้รับการดูแลอย่างแข็งขัน:
- ISO 9001 - ตรวจสอบการใช้งานระบบการจัดการคุณภาพ
- IATF 16949 - มาตรฐานยานยนต์ QMS ที่ระบุการควบคุมการผลิตที่แข็งแกร่ง
- ISO 14001 - ยืนยันโปรโตคอลการจัดการสิ่งแวดล้อม
- OHSAS 18001 - แสดงให้เห็นถึงการมุ่งเน้นไปที่สุขภาพและความปลอดภัยในสถานที่ทำงาน
- EMS 14001 - ตรวจสอบระบบตรวจสอบสิ่งแวดล้อม
- UL 1642-การรับรองความปลอดภัยที่สำคัญสำหรับแบตเตอรี่ลิเธียมไอออน
- UN 38.3 - การทดสอบการขนส่งของ UN สำหรับการขนส่งแบตเตอรี่ลิเธียมที่ปลอดภัย
- ROHS - ยืนยันการปฏิบัติตามสารอันตรายที่ จำกัด
- การเข้าถึง - พิสูจน์ความสอดคล้องกับกฎระเบียบของสารเคมีของสหภาพยุโรป
- QC 080000 - การรับรองภาษาจีนครอบคลุมการผลิตแบตเตอรี่ลิเธียม
- ROHS / FHSA - ข้อ จำกัด ของสารจีนและเกาหลี
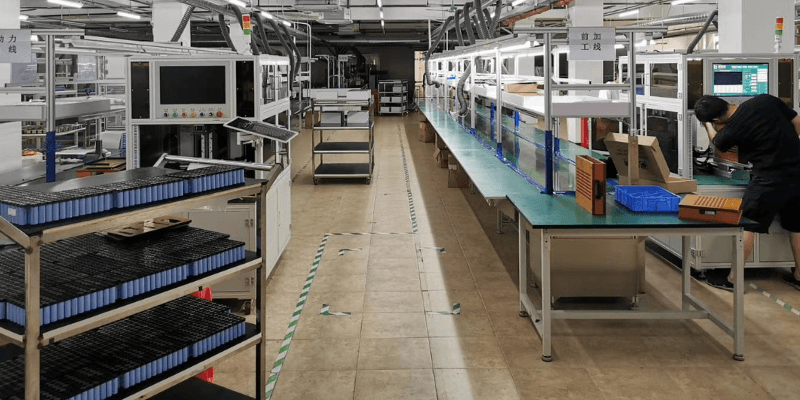
การรับรองควรแสดงอย่างเด่นชัดและตรวจสอบได้ผ่านหน่วยงานที่ออก การตรวจสอบความถูกต้องบ่งบอกถึงการผลิตที่มีคุณภาพสูง
การประเมินความมีชีวิตทางการเงิน
ผู้ผลิตจะต้องจัดแสดงความเหมาะสมทางการเงินที่เปิดใช้งานการเป็นหุ้นส่วนที่ยั่งยืน:
- การจัดอันดับเครดิต - การจัดอันดับเครดิตของบุคคลที่สามที่น่าพอใจแสดงความเสี่ยงล้มละลายต่ำ
- งบการเงิน - ตรวจสอบงบกำไรขาดทุนล่าสุดงบดุลและกระแสเงินสด
- ความสามารถในการทำกำไร - ชอบอัตรากำไรขั้นต้นที่สอดคล้องกันและสุทธิในช่วงหลายปีที่ผ่านมา
- สภาพคล่อง - ตรวจสอบอัตราส่วนสภาพคล่องที่เป็นของแข็งเช่นอัตราส่วนปัจจุบันและอัตราส่วนที่รวดเร็ว
- ระดับหนี้-หลีกเลี่ยง บริษัท ที่มีหนี้สินระยะยาวมากเกินไป
- การคาดการณ์ - งบประมาณและแผนการขยายสิ่งอำนวยความสะดวกสอดคล้องกับความคาดหวังความต้องการของคุณหรือไม่?
ในขณะที่ความท้าทายสำหรับการเริ่มต้นความมั่นคงทางการเงินช่วยลดความเสี่ยงการหยุดชะงัก
เปรียบเทียบราคาและสัญญา
การกำหนดราคาแบตเตอรี่แตกต่างกันอย่างมากตาม:
- ต้นทุนวัสดุ - วัสดุแคโทดเช่นค่าใช้จ่ายผลกระทบโคบอลต์อย่างมีนัยสำคัญ
- มาตราส่วนการผลิต - คำสั่งซื้อจำนวนมากได้รับการกำหนดราคาลดราคา
- การปรับแต่ง-การออกแบบที่ไม่ได้มาตรฐานหรือเครื่องมือเพิ่มค่าใช้จ่าย
- ภูมิศาสตร์ - ประเทศผู้ผลิตส่งผลกระทบต่อค่าแรงและค่าใช้จ่ายด้านสิ่งอำนวยความสะดวก
- การรับประกัน - การรับประกันที่ยาวขึ้นขึ้นราคา
ต้องการข้อตกลงระยะยาวอย่างเป็นทางการพร้อมการรับประกันความสามารถที่เพียงพอ ใช้ประโยชน์จากปริมาณการซื้อที่มากขึ้นเพื่อลดราคา
ผู้ผลิตชุดแบตเตอรี่ลิเธียมในอุดมคติ
พันธมิตรแบตเตอรี่ลิเธียมแบตเตอรี่ที่ดีที่สุดจะแสดงให้เห็นถึงจุดแข็งในพื้นที่สำคัญเหล่านี้:
- ความสามารถในการผลิตและกำลังการผลิต – การผลิตส่วนประกอบการจับคู่ข้อมูลจำเพาะตามปริมาณที่ต้องการ
- ความเป็นผู้นำด้านเทคโนโลยีและความเชี่ยวชาญ – การพัฒนาและผลิตแบตเตอรี่ลิเธียมไอออนขั้นสูงผ่านพนักงานพิเศษ
- การตอบสนองและการสนับสนุน – ส่งมอบหุ้นส่วนที่สูงขึ้นในการพัฒนาการผลิตและหลังการขาย
- กระบวนการคุณภาพ – ใช้การควบคุมกระบวนการที่เข้มงวดและการป้องกันข้อบกพร่อง
- การปฏิบัติตามและความปลอดภัย – การรักษาความปลอดภัยที่สำคัญและการรับรองกฎระเบียบที่สำคัญ
- ฟิตเนสทางการเงิน – แสดงการเติบโตของยอดขายการทำกำไรและการเข้าถึงเงินทุน
- ราคาที่แข่งขันได้ – เสนอราคาราคาที่แข่งขันได้สอดคล้องกับปริมาณการสั่งซื้อ
ด้วยการใช้วิธีการที่เข้มงวดนี้ในการประเมินผู้ผลิตแบตเตอรี่ลิเธียมคุณสามารถสร้างห่วงโซ่อุปทานที่มีประสิทธิภาพซึ่งส่งมอบเซลล์ที่มีคุณภาพสูงสุดและชุดแบตเตอรี่ที่ปรับให้เหมาะกับความต้องการผลิตภัณฑ์และธุรกิจของคุณ
เวลาที่ลงทุนในการตรวจสอบอย่างเหมาะสมและการเลือกผู้ผลิตแบตเตอรี่ลิเธียมไอออนจะจ่ายเงินปันผลผ่านการพัฒนาแบบเร่งความเร็วลดข้อบกพร่องและความเร็วเร่งสู่ตลาด ใช้ประโยชน์จากคู่มือนี้เป็นเฟรมเวิร์กเมื่อทำการตัดสินใจที่สำคัญที่สุดอย่างหนึ่งในการเปิดใช้งานผลิตภัณฑ์ที่ขับเคลื่อนด้วยแบตเตอรี่ลิเธียมไอออนของคุณ
บทความที่เกี่ยวข้อง: