Conclusión clave:
- La fabricación de paquetes de baterías de iones de litio personalizados requiere ingeniería precisa, control de calidad y estándares de seguridad. El proceso implica recopilar requisitos, seleccionar celdas, ingeniería simultánea, creación de prototipos, certificación, planificación de producción y soporte del ciclo de vida.
Desarrollo soluciones de batería personalizadas requiere una amplia experiencia en ingeniería eléctrica, mecánica y de calidad. Si bien es posible que los paquetes de litio disponibles en el mercado no satisfagan completamente las necesidades específicas de potencia, energía, tamaño o funcionalidad de una aplicación, un paquete personalizado creado según requisitos únicos proporciona una solución optimizada.
Sin embargo, el proceso de diseño, certificación y fabricación de paquetes de iones de litio especializados difiere mucho de las opciones estándar. En el siguiente contenido, exploraremos cada paso de fabricación a nivel técnico, que incluye:
- Controles de procesos críticos para garantizar la coherencia
- Técnicas para maximizar el rendimiento dentro de limitaciones.
- Métodos para verificar la calidad y confiabilidad del paquete.
- Protocolos de seguridad al tratar con celdas de iones de litio
- Regulaciones de la industria que rigen la producción de baterías de litio.
Examinemos cómo nuestros equipos de ingenieros expertos abordan la creación de paquetes de baterías de iones de litio personalizados para las aplicaciones más exigentes.
Fases clave en la fabricación de paquetes personalizados
Nuestras principales fases en el desarrollo y producción de paquetes de baterías de iones de litio personalizados incluyen:
- Recogida y diseño de requisitos iniciales.
- Selección y abastecimiento de células en profundidad
- Ingeniería eléctrica y mecánica.
- Validación del diseño de prototipos.
- Pruebas y certificación de seguridad.
- Planificación de la producción y desarrollo de procesos.
- Fabricación de células con estrictos controles de proceso.
- Automatización y accesorios de montaje de baterías de precisión.
- Rigurosas inspecciones de calidad durante toda la fabricación.
- Soporte de instalación y monitoreo de la vida útil del paquete.
A continuación, exploraremos cada fase en detalle, incluidas las consideraciones técnicas exclusivas de la fabricación de soluciones de baterías personalizadas.
Definición de requisitos del producto
Es imperativo capturar minuciosamente los requisitos personalizados de las baterías de litio en un documento de requisitos del producto (PRD) para que los equipos de ingeniería diseñen adecuadamente una solución optimizada. Los parámetros clave que deben definirse incluyen:
Eléctrico
- Capacidad requerida, densidad de energía y Voltaje
- Corriente y potencia máximas para carga máxima
- Objetivo de impedancia y resistencia internas.
- Rangos de temperatura de funcionamiento y necesidades de disipación térmica.
- Características de carga – corriente constante, multietapa, etc.
Mecánico
- Limitaciones de peso y tamaño
- Puntos de montaje, marcos y espacios libres
- Selecciones de materiales de gabinete
- Necesidades de sellado ambiental y clasificación de protección de ingreso (IP)
- Requisitos de resistencia a vibraciones, golpes y aplastamientos.
Funcional
- Ciclo estimado y vida útil del calendario en el DOD definido
- Límites de tasa de autodescarga inactiva
- Interfaces de comunicación necesarias y registro de datos
- Cualquier sensor o electrónica adicional necesaria
Calidad & Programa
- Tasas de defectos objetivo y margen de error
- Certificaciones obligatorias como UL 1642 o Y 38.3
- Restricciones presupuestarias y límites máximos de costos
- Programe expectativas e hitos
La recopilación cuidadosa de los requisitos evita cambios de diseño en las últimas etapas.
Selección de celdas de iones de litio de alto rendimiento
La base de cualquier paquete de baterías de iones de litio personalizado radica en la selección de las celdas integradas. Nuestra selección de celdas para paquetes personalizados incluye:
- Determinación de la química óptima de las celdas de iones de litio: níquel, manganeso y cobalto (NMC), fosfato de litio y hierro (LFP), etc.
- Evaluación de los formatos de celda disponibles: cilíndrico, de bolsa o prismático
- Comprobación de la capacidad de la celda, el historial de calidad y la capacidad de producción.
- Obtener muestras de células cilíndricas y laminadas de proveedores para realizar pruebas directas si es necesario
- Comparación de puntos de referencia de rendimiento celular – densidad de energía, potencia específica, ciclo de vida, seguridad
- Finalizando la celda optimizando compensaciones clave – costo, entrega de energía, vida útil, factor de forma
Los avances en las celdas de iones de litio continúan ampliando los límites del rendimiento año tras año. Aprovechar la tecnología celular de última generación es crucial para maximizar las capacidades de los paquetes personalizados.

Ingeniería Eléctrica y Mecánica
Se necesita ingeniería eléctrica y mecánica simultánea para optimizar el diseño del paquete personalizado dentro de las limitaciones.
Electrotecnia
- Diseño de geometrías de barras colectoras y métodos de conexión para lograr la capacidad de corriente requerida y minimizar la resistencia.
- Enrutamiento de arneses de cableado para permitir la capacidad de fabricación y servicio
- Tamaño del fusible y del relé de la batería para brindar protección contra fallas hasta la corriente máxima del paquete.
- Ubicaciones y cantidades de termistores para un monitoreo detallado de la temperatura
- Optimización de las interfaces de sensores y comunicaciones para los periféricos necesarios
Ingeniería Mecánica
- Selección de materiales para gabinetes que equilibran costo, resistencia, peso y capacidad de fabricación
- Interno componente espaciado que permite un flujo de aire suficiente para la gestión térmica
- Puntos de montaje, marcos y tirantes para la rigidez estructural requerida.
- Diseño de retenedor de celda, arnés y sujetador que evita daños por golpes o vibraciones.
- Métodos de interconexión: soldadura, soldadura fuerte, fijación mecánica.
- Modelado térmico para desarrollar canales de refrigeración, disipadores de calor y aislamiento.
La combinación de ingeniería eléctrica y mecánica es esencial para evitar compensaciones subóptimas en el diseño de baterías personalizadas.
Validación de diseño mediante prototipos
Construir y evaluar múltiples prototipos de diseño es imprescindible para el desarrollo de baterías de litio personalizadas. La creación de prototipos permite:
- Pruebas de forma y ajuste mecánicos utilizando carcasas impresas en 3D
- Confirmar que el rendimiento eléctrico cumple con los requisitos
- La validación de la gestión térmica mantiene la temperatura de las celdas
- Refinamiento de la ubicación, los controles y los algoritmos de los sensores BMS
- Calificación de resistencia a vibraciones con prueba de mesa vibratoria
- Verificación de la seguridad del diseño mediante análisis de modos y efectos de falla
- Mejora de la capacidad de fabricación basada en evaluaciones de ensamblaje
La creación repetida de prototipos descubre fallas que no son evidentes durante la ingeniería asistida por computadora.
Certificaciones de seguridad obligatorias
La adquisición de certificaciones reglamentarias y de seguridad verifica el cumplimiento del paquete:
- UL 1642: certificación crítica para la seguridad de las baterías de iones de litio de Underwriters Laboratories
- IEC 62133: norma internacional que especifica los requisitos de seguridad para celdas secundarias selladas portátiles
- Y 38.3 – Metodología de prueba de la ONU para el transporte seguro de baterías de litio
- Marcado CE: confirma la conformidad con las normas europeas de salud, seguridad y medio ambiente.
- FCC: valida la compatibilidad electromagnética y los límites de interferencia
- RoHS – Directiva de la Unión Europea sobre restricción de sustancias peligrosas
Las pruebas las realizan laboratorios acreditados que emiten certificaciones formales una vez que se cumplen los requisitos.
Planificación de la producción y refinamiento de procesos
Una meticulosa planificación inicial evita errores no forzados durante la fabricación:
- Creación de listas de materiales completas que especifiquen proveedores y piezas aprobados.
- Diseño de accesorios de montaje, plantillas y herramientas para una producción a prueba de errores.
- Definición de estaciones de prueba automatizadas y manuales necesarias para el control de procesos.
- Desarrollar instrucciones detalladas de montaje y prueba del operador.
- Análisis de sitios de fabricación para necesidades de espacio, energía, medio ambiente y seguridad.
- Planificación de la logística de la cadena de suministro para componentes e inventario de células.
- Reclutamiento y capacitación de técnicos competentes en fabricación de células y ensamblaje de paquetes.
- Instituir controles de procesos estadísticos que rastreen métricas clave de desempeño.
Una planificación cuidadosa del proceso se traduce en resultados de calidad.
Pasos rigurosos de control de calidad
La calidad constante se verifica mediante inspecciones antes, durante y después de la producción:
Control de calidad entrante (IQC): garantiza que las materias primas y los componentes cumplan con las especificaciones
- Inspección de celdas de iones de litio entrantes: verificación de capacidades, perfiles de voltaje y clasificación
- Comprobación de placas, láminas y separadores antes de la fabricación de células.
- Prueba de lotes de placas de circuito impreso para detectar defectos
- Validación de piezas del paquete como carcasas y conectores.
Control de calidad en el proceso (IPQC): mantiene la capacidad y la estabilidad del proceso.
- Control estadístico de procesos (SPC) que rastrea parámetros críticos
- Recuento de defectos, tasas de muestreo y mejora continua
- Inspección de celdas y paquetes en cada paso del ensamblaje.
- Auditorías de procesos que garantizan que se sigan los procedimientos.
Control de calidad del producto final (FPQC): confirma la calidad del paquete antes del envío
- Inspección dimensional contra planos.
- Capacidad del paquete de prueba, resistencia interna y aumento de temperatura.
- Inspección por rayos X de conexiones internas.
- Validar la construcción y el diseño – térmicas, holguras, etc.
- Ejecute pruebas funcionales bajo carga para verificar el rendimiento.
Un control de calidad sólido es crucial para establecer la repetibilidad del proceso y eliminar defectos.
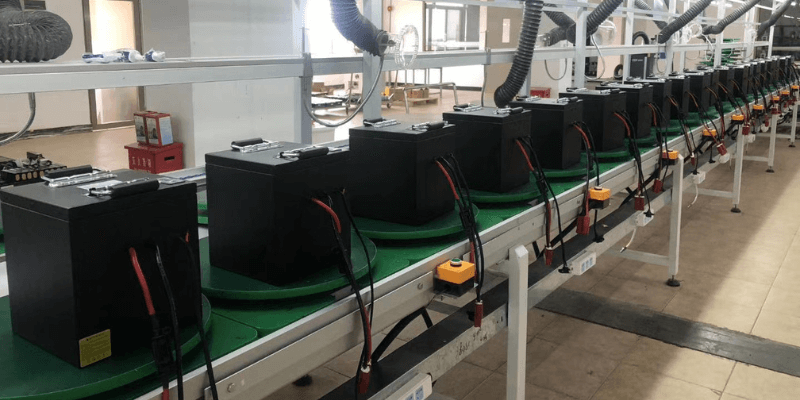
Fabricación de celdas de iones de litio
Producir celdas de iones de litio prismáticas o de bolsa con la consistencia necesaria para ensamblaje del paquete exige entornos y procesos estrictamente controlados. Los pasos de fabricación celular incluyen:
- Mezclando – Formulación de lodos de cátodos y ánodos con estricto control de composición
- Recubrimiento: aplicación uniforme de recubrimientos de electrodos a láminas del colector de corriente
- Calandrado: ajuste preciso del espesor del recubrimiento del electrodo
- corte – Cortar láminas de electrodos en anchos específicos
- Bobinado/Apilamiento: bobinado de electrodos cilíndricos o apilados en capas con separador
- Soldadura con lengüeta: soldadura de terminales de celda a lo largo de los bordes del electrodo
- Llenado de electrolito: inyección de electrolito líquido formulado en la celda
- Formación – Ciclo inicial de carga-descarga que activa los electrodos.
- Envejecimiento: asentamiento y estabilización de células antes de realizar la prueba.
- Clasificación: agrupación de celdas en contenedores por capacidad, impedancia y perfil de voltaje probados
Mantener la capacidad del proceso proporciona la consistencia celular vital para el ensamblaje del paquete. Las variaciones de celdas pequeñas se agravan cuando se multiplican por miles en un paquete.
Proceso de ensamblaje del paquete de baterías
El ensamblaje de celdas y componentes en un paquete de baterías resistente requiere una construcción meticulosa:
- Emparejar celdas por grado para una variación mínima
- Interconexión eléctrica de celdas en serie mediante soldadura o sujetadores.
- Asegurar celdas en accesorios personalizados durante el ensamblaje del paquete
- Enrutamiento y fijación de mazos de cables de alto voltaje
- Montaje e interfaz térmica de placas electrónicas de potencia.
- Aplicación de material de interfaz térmica entre celdas.
- Fijación de barras colectoras con especificaciones de par exactas
- Integración de componentes en cajas de metal o plástico.
- Tableros de revestimiento conformado para la protección del medio ambiente
- Conjuntos de encapsulado con epoxi o silicona para rigidez estructural.
- Torque de auditoría de sujetadores durante el proceso para verificar la integridad del ensamblaje
Cada paso de producción debe cumplir con procesos y criterios de aceptación estrictamente definidos para garantizar productos finales confiables.
Consideraciones de instalación, operación y ciclo de vida
Una vez producidos, es fundamental soportar adecuadamente los paquetes durante toda su vida útil:
- Proporcionar prácticas recomendadas de instalación detalladas para integrar los paquetes correctamente
- Registro de datos integrado que monitorea el uso, indicadores de advertencia y códigos de falla
- Analizar datos de campo para mejorar continuamente diseños futuros.
- Entrega de actualizaciones de firmware para ampliar capacidades y corregir errores
- Ofrecer servicios de reparación, reacondicionamiento o reciclaje de paquetes caducados.
- Hacer circular proactivamente información de seguridad sobre el manejo adecuado, los riesgos y las precauciones.
Esta mentalidad sobre el ciclo de vida maximiza el retorno de la inversión en baterías de iones de litio personalizadas.
Consideraciones de seguridad de las baterías de iones de litio
Trabajar con celdas y baterías de iones de litio requiere protocolos de seguridad rigurosos dados los riesgos de inflamabilidad si se manipulan incorrectamente. Las precauciones clave de fabricación incluyen:
- Pasivar restos de electrodos y celdas gastadas en contenedores de arena antes de su eliminación.
- Delimitación de áreas designadas para almacenamiento de litio con gabinetes y supresión ignífugos.
- Hacer cumplir el equipo de protección personal como guantes, gafas y ropa resistente al fuego.
- Evitar la carga de la celda cerca de materiales o vapores inflamables.
- Utilizar únicamente herramientas no conductoras diseñadas para el montaje de baterías de litio.
- Prohibir joyas o ropa holgada cerca de maquinaria en movimiento.
- Capacitar al personal de fabricación de celdas y ensamblaje de paquetes sobre seguridad de baterías de litio
El estricto cumplimiento de las prácticas de seguridad de iones de litio protege al personal y las instalaciones.
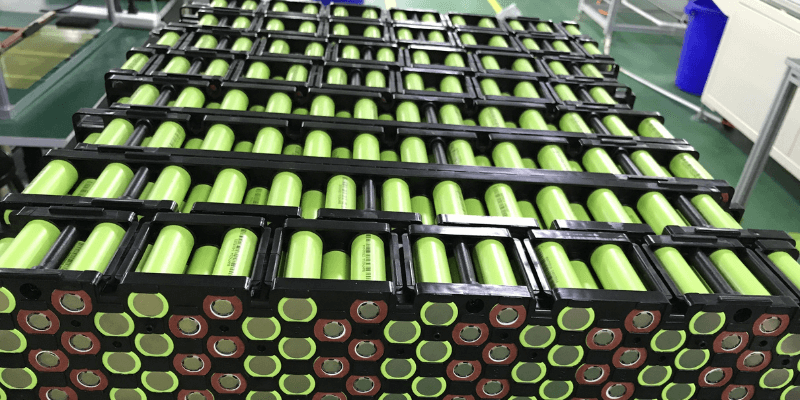
Al abordar el desarrollo de baterías de iones de litio especializadas como un desafío de ingeniería multifuncional que requiere una validación rigurosa, las empresas pueden crear con éxito paquetes personalizados que desbloqueen capacidades de rendimiento únicas.
Artículos relacionados:
- Nuevas tendencias en diseños de paquetes de baterías de litio personalizados
- Causas de falla del paquete de baterías de litio
- Cómo elegir el mejor tablero de protección para paquetes de baterías de litio
- Cómo elegir el mejor fabricante de baterías de litio
- Los 10 principales fabricantes de baterías de litio en China