重要なポイント:
- カスタム リチウムイオン バッテリー パックの製造には、正確なエンジニアリング、品質管理、および安全基準が必要です。このプロセスには、要件の収集、セルの選択、コンカレント エンジニアリング、プロトタイピング、認証、生産計画、ライフサイクル サポートが含まれます。
現像 カスタムバッテリーソリューション 電気、機械、品質エンジニアリングにわたる広範な専門知識が必要です。既製のリチウム パックはアプリケーションの特定の電力、エネルギー、サイズ、機能のニーズを完全には満たさない場合がありますが、独自の要件に合わせて構築されたカスタム パックは最適化されたソリューションを提供します。
ただし、特殊なリチウムイオン パックの設計、認証、製造のプロセスは、標準オプションとは大きく異なります。次のコンテンツでは、次のような各製造ステップを技術レベルで説明します。
- 一貫性を確保するための重要なプロセス制御
- 制約内でパフォーマンスを最大化するテクニック
- パックの品質と信頼性を検証する方法
- リチウムイオン電池を取り扱う際の安全プロトコル
- リチウム電池の製造を管理する業界規制
当社の専門エンジニアリング チームが、最も要求の厳しい用途に合わせたカスタム リチウムイオン バッテリー パックの構築にどのようにアプローチしているかを見てみましょう。
カスタム パック製造の主要な段階
カスタム リチウムイオン バッテリー パックの開発と製造における主な段階は次のとおりです。
- 初期要件の収集と設計
- 綿密なセルの選択と調達
- 電気および機械工学
- プロトタイピング設計の検証
- 安全性試験と認証
- 生産計画とプロセス開発
- 厳密なプロセス管理によるセル製造
- 精密なバッテリー組立治具と自動化
- 製造全体にわたる厳格な品質検査
- 設置サポートとパック寿命の監視
次に、カスタム バッテリー ソリューションの製造に特有の技術的考慮事項を含め、各フェーズを詳しく説明します。
製品要件の定義
エンジニアリング チームが最適化されたソリューションを適切に設計するには、カスタム リチウム バッテリー要件を製品要件文書 (PRD) で徹底的に把握することが不可欠です。定義する必要がある主なパラメータは次のとおりです。
電気
- 必要な容量、エネルギー密度、 電圧
- 最大負荷時のピーク電流と電力
- ターゲットの内部インピーダンスと抵抗
- 動作温度範囲と熱放散のニーズ
- 充電特性 – 定電流、多段など
機械式
- 重量とサイズの制限
- 取り付けポイント、フレーム、およびクリアランス
- エンクロージャ材質の選択
- 環境シールのニーズと侵入保護 (IP) 評価
- 振動、衝撃、耐圧潰性の要件
機能的
- 定義された DOD での推定サイクルおよびカレンダー寿命
- アイドル時自己放電率制限
- 必要な通信インターフェースとデータロギング
- 追加のセンサーや電子機器が必要な場合
品質 & プログラム
- 目標の欠陥率と誤差の範囲
- UL 1642 や そして38.3
- 予算の制約とコストの上限
- 期待とマイルストーンのスケジュールを立てる
要件を慎重に収集することで、後期段階での設計変更を防ぎます。
高性能リチウムイオン電池の選択
カスタム リチウムイオン バッテリー パックの基礎は、統合されたセルの選択にあります。カスタム パック用のセルの選択には次のことが含まれます。
- 最適なリチウムイオン電池の化学的性質の決定 – ニッケル・マンガン・コバルト (NMC)、リン酸鉄リチウム (LFP)など。
- 利用可能なセル形式の評価 – 円筒形、ポーチ形、または角柱形
- セルの能力、品質実績、生産能力の確認
- 必要に応じて直接テストを行うために、ベンダーから円筒セルとラミネートセルのサンプルを調達します。
- セルの性能ベンチマークの比較 – エネルギー密度、比出力、サイクル寿命、安全性
- 主要なトレードオフを最適化してセルを完成させる – 料金、電力供給、寿命、フォームファクター
リチウムイオン電池の進歩により、性能の限界は年々拡大し続けています。カスタムパックの機能を最大化するには、最先端のセルテクノロジーを活用することが重要です。

電気機械工学
制約内でカスタム パック設計を最適化するには、電気工学と機械工学を同時に行う必要があります。
電気工学
- 必要な電流容量を達成し、抵抗を最小限に抑えるためのバスバーの形状と接続方法を設計します。
- 製造性と保守性を可能にするワイヤーハーネスのルーティング
- パック最大電流まで障害保護を提供するヒューズとバッテリーリレーのサイジング
- きめ細かい温度監視のためのサーミスターの配置と数量
- センサーと通信インターフェイスを必要な周辺機器に最適化
機械工学
- コスト、強度、重量、製造容易性のバランスを考慮したエンクロージャ材料の選択
- 内部 成分 熱管理のために十分な空気の流れを確保できる間隔
- 必要な構造剛性を確保するための取り付けポイント、フレーム、ブレース
- 衝撃や振動による損傷を防ぐセルリテイナー、ハーネス、ファスナーの設計
- 相互接続方法 – 溶接、はんだ付け、機械的固定
- 熱をモデル化して冷却チャネル、ヒートスプレッダー、断熱材を開発する
カスタムバッテリー設計における次善のトレードオフを回避するには、電気工学と機械工学の融合が不可欠です。
プロトタイピングによる設計の検証
カスタム リチウム電池の開発には、複数の設計プロトタイプを構築して評価することが必須です。プロトタイピングにより次のことが可能になります。
- 3D プリントされた筐体を使用した機械的形状と適合性のテスト
- 電気的性能が要件を満たしていることを確認する
- セル温度を維持する熱管理を検証する
- BMS センサーの配置、制御、アルゴリズムの改良
- シェーカーテーブル試験による耐振動性の評価
- 故障モードと影響解析による設計の安全性の検証
- 組立評価による製造性の向上
プロトタイピングを繰り返すことで、コンピュータ支援エンジニアリングでは気づかなかった欠陥が明らかになります。
必須の安全認証
安全性および法規制の認証を取得することで、パックのコンプライアンスが検証されます。
- UL 1642 – Underwriters Laboratories によるリチウムイオン電池の安全性に関する重要な認証
- IEC 62133 – ポータブル密閉二次電池の安全要件を指定する国際規格
- そして38.3 – リチウム電池の安全な輸送のための国連の試験方法
- CE マーキング – 欧州の健康、安全、環境基準への適合を確認します。
- FCC – 電磁適合性と干渉制限を検証します。
- RoHS – 欧州連合の有害物質制限指令
テストは、要件が満たされた後に正式な証明書を発行する認定研究所によって実行されます。
生産計画とプロセスの改良
綿密なフロントエンド計画により、製造中の不可逆的なエラーを防止します。
- 承認されたベンダーと部品を指定した包括的な部品表の作成
- 間違いのない生産のための組立治具、治具、ツールの設計
- プロセス制御に必要な自動および手動テストステーションの定義
- 詳細なオペレーターの組み立ておよびテスト手順の作成
- 製造現場のスペース、電力、環境、安全性のニーズを分析
- コンポーネントとセル在庫のサプライチェーンロジスティクスの計画
- 有能なセル製造およびパック組立技術者の採用とトレーニング
- 主要なパフォーマンス指標を追跡する統計的プロセス管理の導入
思慮深いプロセス計画が高品質の結果につながります。
厳格な品質管理手順
一貫した品質は、製造前、製造中、製造後の検査を通じて検証されます。
受入品質管理 (IQC) – 原材料とコンポーネントが仕様を満たしていることを確認します
- 入荷したリチウムイオンセルの検査 - 容量、電圧プロファイル、およびグレードの検証
- セル製造前のプレート、フォイル、セパレーターの検査
- プリント基板ロットの欠陥のテスト
- ハウジングやコネクタなどのパック部品の検証
工程内品質管理 (IPQC) – プロセスの能力と安定性を維持します
- 重要なパラメータを追跡する統計的プロセス制御 (SPC)
- 欠陥数、サンプリングレート、継続的改善
- 各組み立てステップでのセルとパックの検査
- 手順が遵守されていることを確認するプロセス監査
最終製品品質管理 (FPQC) – 出荷前にパックの品質を確認します
- 図面との寸法検査
- パックの容量、内部抵抗、温度上昇の試験
- 内部接続部のX線検査
- 構造が設計を満たしていることを検証する – サーマル、クリアランスなど。
- 負荷をかけた状態で機能テストを実行してパフォーマンスを検証する
プロセスの再現性を確立し、欠陥を排除するには、堅牢な品質管理が不可欠です。
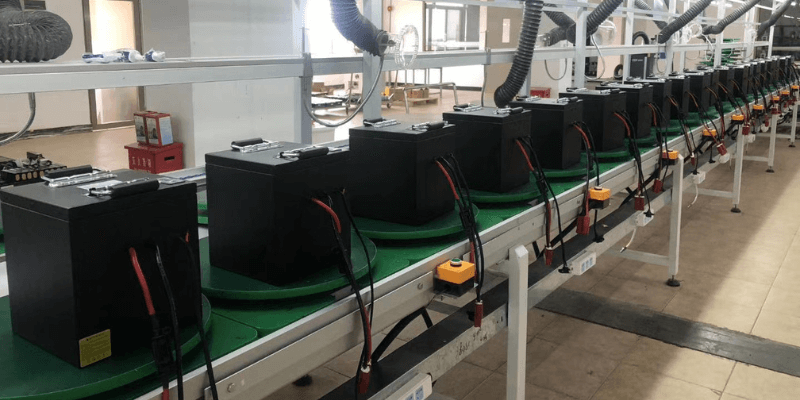
リチウムイオン電池の製造
必要な一貫性を備えた角形またはパウチ型リチウムイオン電池を製造します。 パックアセンブリ 厳密に管理された環境とプロセスが義務付けられています。セルの製造手順は次のとおりです。
- 混合 – 厳密な組成制御によるカソードおよびアノードのスラリーの配合
- コーティング – 集電箔に電極コーティングを均一に塗布します。
- カレンダー加工 – 電極コーティングの厚さを正確に調整
- スリッティング – 電極シートを特定の幅に切断する
- 巻き付け/積層 – 円筒状の電極を巻き付けるか、セパレーターを備えた層状電極を積み重ねる
- タブ溶接 – 電極端に沿ってセル端子を溶接します。
- 電解質の充填 – 配合された液体電解質をセルに注入します
- 形成 - 電極を活性化する初期充放電サイクル
- エージング – テスト前のセルの慣らしと安定化
- グレーディング – テストされた容量、インピーダンス、電圧プロファイルに基づいてセルをビンにグループ化します。
プロセス能力を維持することで、パックの組み立てに不可欠なセルの一貫性が実現します。小さなセルのバリエーションは、パック内で数千個増加するとさらに大きくなります。
バッテリーパックの組み立て工程
セルとコンポーネントを組み立てて耐久性の高いバッテリー パックを作成するには、次のような細心の注意を払った構造が必要です。
- グレードごとにセルを一致させてばらつきを最小限に抑える
- 溶接または留め具を使用してセルを直列に電気的に相互接続する
- パックの組み立て中にカスタム治具にセルを固定する
- 高圧ワイヤーハーネスの配線と固定
- パワーエレクトロニクスボードの取り付けと熱インターフェイス
- セル間にサーマルインターフェースマテリアルを適用
- 正確なトルク仕様でバスバーを取り付ける
- コンポーネントを金属またはプラスチックの筐体に統合する
- 環境保護のための絶縁保護コーティングボード
- 構造的剛性を高めるためにエポキシまたはシリコーンを使用したポッティングアセンブリ
- プロセス中にファスナーにトルクを監査して、アセンブリの完全性を検証します
信頼性の高い最終製品を保証するには、各製造ステップが厳密に定義されたプロセスと合格基準に従う必要があります。
インストール、運用、ライフサイクルに関する考慮事項
製造後は、耐用年数を通じてパックを適切にサポートすることが最も重要です。
- パックを正しく統合するための詳細なインストールのベスト プラクティスを提供する
- オンボードデータロギングの使用状況、警告フラグ、障害コードの監視
- 現場データを分析して将来の設計を継続的に改善する
- 機能を拡張し、バグを修正するためのファームウェア アップデートの提供
- 期限切れパックの修理、再調整、リサイクルサービスの提供
- 適切な取り扱い、リスク、注意事項などの安全情報を積極的に発信
このライフサイクルの考え方により、カスタム リチウムイオン バッテリーへの投資の ROI が最大化されます。
リチウムイオン電池の安全性に関する考慮事項
リチウムイオンセルおよびバッテリーを扱うには、不適切に取り扱われた場合の引火リスクを考慮した厳格な安全プロトコルが必要です。主な製造上の注意事項は次のとおりです。
- 廃棄する前に電極のスクラップと使用済みセルを砂箱に入れて不動態化する
- 指定されたリチウム貯蔵エリアを耐火キャビネットと抑制装置で区切る
- 手袋、ゴーグル、難燃性衣服などの個人用保護具の強化
- 可燃物や蒸気の近くでのセルの充電を避ける
- リチウム電池組み立て用に設計された非導電性ツールのみを使用してください
- 動いている機械の近くで宝石類やゆったりした衣類を禁止する
- セル製造およびパック組立スタッフにリチウム電池の安全性に関するトレーニングを実施する
リチウムイオンの安全慣行を厳守することで、人員と施設を保護します。
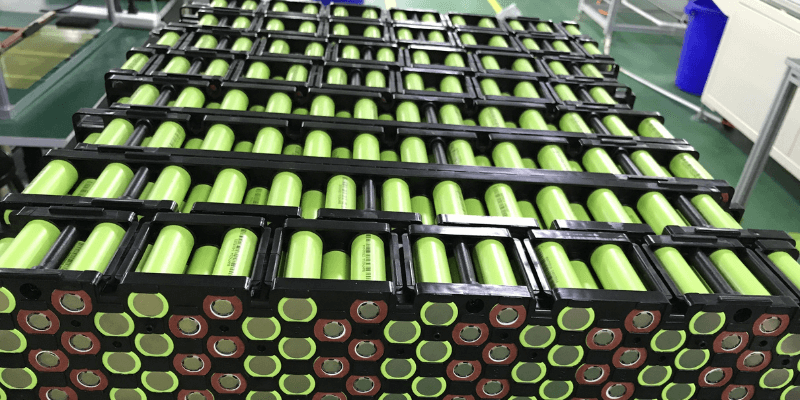
厳密な検証を必要とする部門横断的なエンジニアリング課題として特殊なリチウムイオン電池開発に取り組むことで、企業は独自のパフォーマンス機能を解き放つカスタム パックを構築することに成功できます。
関連記事: