Creating a maßgeschneiderter Akku involves finding the right balance of performance, safety, and adherence to industry standards. Here’s a breakdown of the key considerations, along with insider tips to assist engineers and product developers.
Determining Power Requirements
When it comes to power needs, they essentially determine a battery’s voltage, capacity, and Energiedichte. Here’s what you need to keep in mind:
Application-Specific Loads
Different applications have different needs. Electric vehicles (EVs), for instance, require high power density (think 50C discharge rates), whereas medical devices focus on maintaining a steady voltage.
Spannungsanpassung
Custom battery packs often combine cells in series or parallel setups. So, a 48V system might use around 13–14 LiFePO4 cells at 3.2V each or 14 NMC cells at 3.7V each.
Energy Density Optimization
If you’re aiming to reduce pack size with high-capacity cells (up to 40Ah per cell), remember you’ll need advanced Thermalmanagement.
Peak vs. Continuous Power
Hoch Kiste cells (like those at 50C) are ideal for drones needing quick energy bursts, while energy storage systems prioritize lasting power over short spurts.
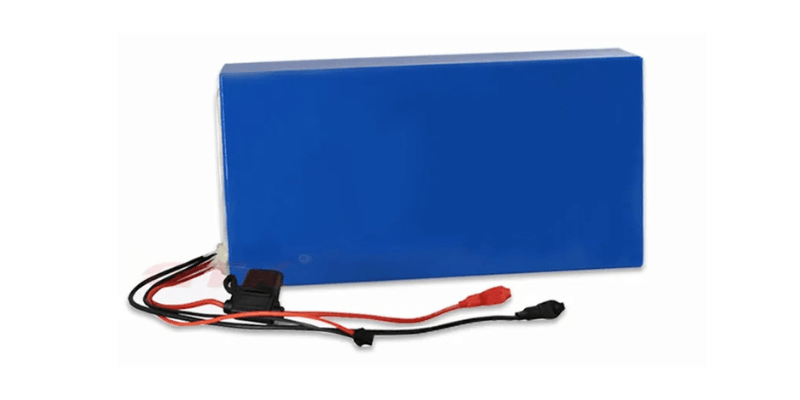
Calculating Charge Requirements
Charge parameters significantly influence the efficiency and safety of charging. Here’s the scoop:
Charging Protocols
For fast-charging systems like 800V setups, your Batteriemanagementsystem (BMS) must handle communication protocols such as CAN or SMBus.
Charge Rate
It’s important not to exceed what your cells can handle, like sticking to 1C for LiFePO4 cells or keeping it at 0.5C for some NMC cells.
Thermal Constraints
Fast charging generates more heat, so using liquid cooling or phase-change materials is essential to maintain temperatures below 45°C.
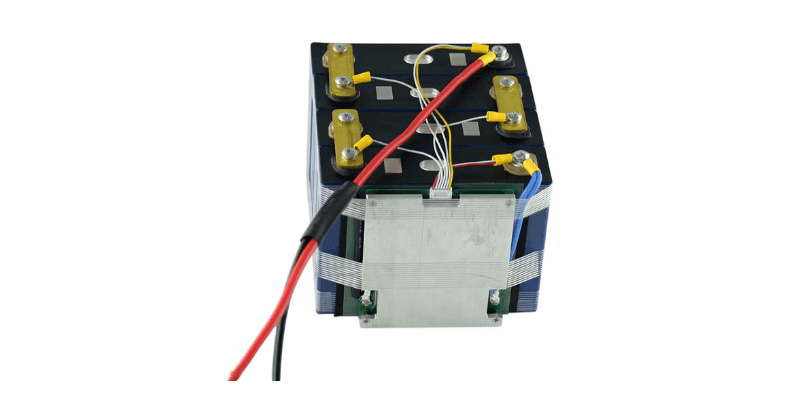
Providing Safety Features
Safety is essential, with no compromises. Here are key safety features to consider:
BMS Protection Layers
- Overvoltage/undervoltage cutoffs (e.g., a maximum of 3.65V for LiFePO4).
- Quick short-circuit detection (less than 1ms response time).
- Cell balancing, whether passive or active, to maintain even voltage levels.
Thermal Management
- Liquid cooling for high-power packs like EV batteries.
- Self-heating technology to ensure smooth operation in the cold.
Mechanical Safety
- Enclosures with IP67 ratings to protect against dust and water.
- Explosion vents and flame-retardant materials, such as UL94 V0-rated plastics.

Designing Material & Enclosure Requirements
Materials impact the durability, weight, and heat efficiency of products.
For Enclosure
- Aluminum alloys offer strength while remaining lightweight.
- Thermoplastics like PA66-GF30 enhance vibration resistance and block EMI.
For Thermal Management
Silicone pads or epoxy resins excel at dissipating heat.
To reduce weight, SABIC’s NORYL resins can make enclosures 40% lighter than aluminum.
Pro tip: Before finalizing your design, use 3D-printed mockups to evaluate space constraints and thermal flow efficiency.
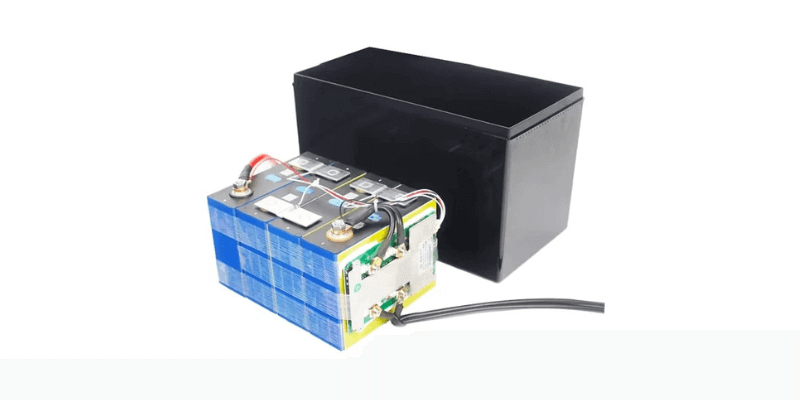
Certification Requirements
Keeping up with compliance is crucial for entering markets and protecting against liabilities. Here’s the lowdown:
Global Standards
- UN38.3: Ensures safe transportation.
- ISO 12405: Guarantees EV battery performance.
- UL 2580 (U.S.) and CE (EU): Focus on electrical safety.
Regional Compliance
- In India, BIS mandates fire-resistant cases and EMI shielding.
- China’s GB/T 31467 focuses on preventing thermisches Durchgehen.
Audit Checklist
Ensure coverage of cell-level certifications like IEC 62133 and pack-level tests such as crush and vibration checks.

Abschluss
Custom battery packs require a systems-level approach.
- Prioritize safety with strong BMS and thermal designs, optimize power/charge parameters, and select materials that balance weight and durability.
- Use emerging technologies like solid-state electrolytes and modular architectures.
- Engage certified testing labs early to ensure compliance and avoid costly redesigns.
Addressing these factors helps engineers deliver high-performance packs that meet industry standards.